Let’s say you want to build an imaging system, but you want to attach 2 cameras for time-correlated 2 channel imaging. The limiting factor for such an arrangement is usually cost, that cost being $10,000 USD per camera means $20,000 for such a setup! A result of this is most researchers end up not using time correlation at such an accuracy, and resort to filter cube switching or emission wheels. Enter the new release of Micro-Manager drivers for Pt. Grey cameras. Through the hard work of Nico Stuurman, Micro-Manager now supports most of the low cost USB cameras offered by this machine vision camera manufacturer. Kurt Thorn has an excellent report on his blog with performance data from one of Pt. Grey’s CMOS cameras.
The key point? Most microscopy cameras start @ $6,000 USD, and go up from there. By comparison, Pt Grey cameras usually run less than $1,000 USD!
So why is it that such a camera can cost 1/10 of a typical microscopy camera? The major cause is the ongoing market cycle of entrenched mature products and services, vs. disruptive technologies and products. Clayton Christensen explains the nature of this process in his excellent book, “The Innovator’s Dilemma“, but let’s look at the top 2 reasons for the price delta.
Cooling: Most of the big camera manufacturers chase each other on performance specifications. If you’ve attempted to purchase one of these cameras through an on-site demo, you’ve likely heard the “spec war” sales pitch, wherein camera company A explains the important numeric advantages (quantum efficiency, read noise, dark current, etc) over companies B, C etc. Of course, this rises out of a need to improve a camera’s performance as much as possible, to win sales. While this is all great for both product variation and for economic advantage (better product at a lower cost through competition), it assumes that the people driving these specs actually understand how important they are to the end user. In the past, dark noise was an easy problem to “one up” on performance. How? Simply cool the sensor! So peltier coolers (thermoelectric plates) were attached to the backside of sensors, with large radiators used to vent drawn heat on the back of the camera. This gave us heavy, large cameras with very low dark current of 0.03 electrons per pixel per second. But how does this relate to the average user? Normal exposure times are < 1 sec. Read noise levels on quiet cameras are ~ 3 electrons. So one would need to capture an image for an exposure time of 3 / 0.01 = 300 seconds, in order to reach a thermal issue with the camera! But the better spec gave an advantage to sales, and therefore this performance was considered standard in the industry, even though 99% of end users don’t need it.
Of course, other issues pop up when adding such extreme cooling. One is condensation. Because these chips would be cooled to -30c or lower, condensation loved to form on the face of the sensor, which obscures the image, and shorts the sensor. As a result, a vacuum sealed window must be placed around the sensor. Dry nitrogen may be back-filled into the chamber, but in the end, you have a chamber waiting for a leak. The manufacturing process is costly. All of this adds up to $$$$, which transfers down to the customer. Finally this trend is changing. Today, Hamamatsu, Pt Grey and others offer ambient (read un-cooled) camera options, resulting in substantial cost savings to customers.
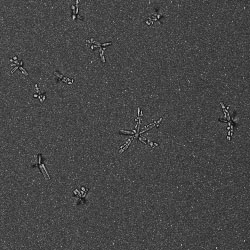
Manufacturing: CCD sensors were initially produced on accident. RAM designers found that configurations of chip layouts were light sensitive, and as a result discovered they could be used to detect light in an array. Soon after CCDs began a strong fabrication growth, conventional memory switch from serial addressed layouts to dynamically addressed layouts. This resulted in CCD manufacturers being able to only build CCD chips, and not other, newer forms of memory. Single-use costs of such facilities caused prices to stay relatively high, as how many end-users require monochrome sensors, high sensitivity, precision, etc etc? Most consumers of sensor technology want to see a pretty picture on a phone! So CCD sensor production became a high cost problem. CMOS technology unlocked this problem, allowing conventional memory production houses to build CMOS sensors. As sensor production expanded, “modular” sensor packages went from the exception to the rule for the majority of cameras sold today. In the past, camera companies purchased a “chip” which had only the sensor, and access pins attached to it. It was required for the camera company to add a window, seal or other protective assembly, readout electronics, etc. Beginning with the ICX series from Sony, things changed. Instead of purchasing only a sensor, you could purchase a pre-built package right from the sensor manufacturer, including a complete window, and in some cases, the ADC and clocks all ready for use. Both of these changes in how sensors are produced have given rise to two new entrants in the camera market – low cost camera companies, who do as minimal work as required to get a camera out for sale, and more manufacturing houses capable of producing sensors. All this adds up to more choice for the consumer at a lower, more competitive price.
So what does this mean for you? Check out the Pt Grey camera line! It’ll save you a bundle on your imaging system, and may unlock your options for more multi-channel imaging!
-Austin
Comments
One response to “Pt Grey Camera Driver for MicroManager unleashes low-cost microscopy”
Hi there,
I am working with a company that supplies Point Grey cameras. We have a number of customers that would be interested to read your blog. Do you mind if we share this link and your findings with them?
Thanks:)